Our proven process is a structured and effective approach that we’ve developed from years of successful engagements with clients across the country. With internal communication and planning first, our team follows well-defined methodology to reduce the risk of errors and increase overall efficiency leading to more effective solutions to our clients’ challenges. We communicate with our clients through each step of the consultative process to manage expectations for all project stakeholders. The framework ensures our clients receive the highest level of service experience and quality results consistently and on time.
7G’s Proven Process helps enhance the service experience, bring the most value to the engagement, and contribute to the long-term success of our partnership.
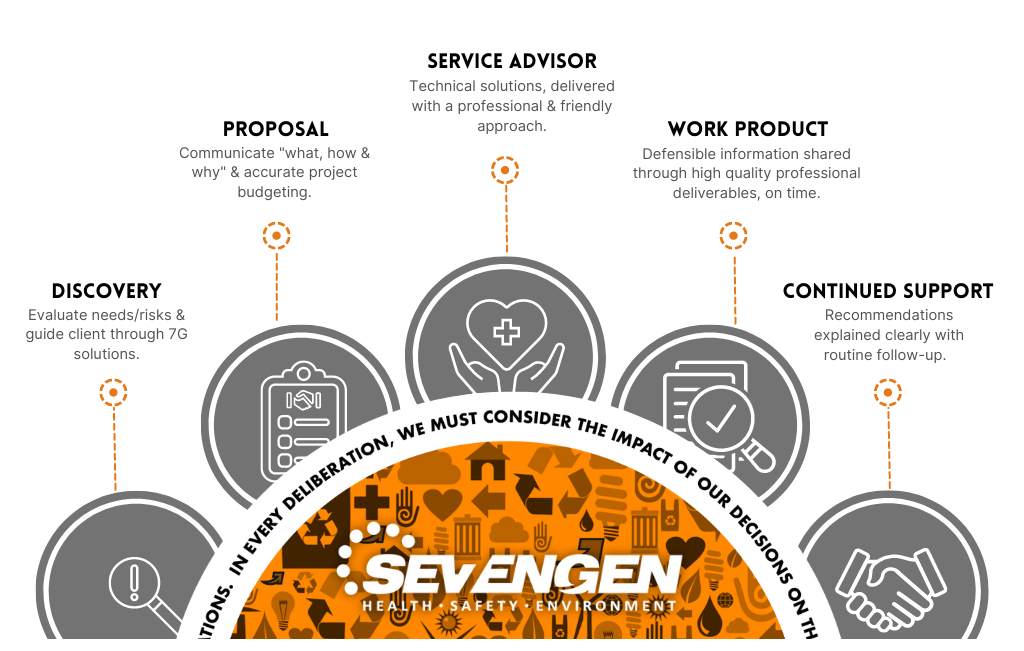
All of these factors, combined with our ability to provide the highest quality service with a focus on expedient and quality consultation, make SevenGen the ideal partner for any of your HSE needs.
Contact 7G Today
At SevenGen, we bring our technical expertise and passion for problem solving to help your organization stay safe, healthy, environmentally responsible and complaint. Schedule a discovery call with one of our HSE experts today.